Trenchless studies, design & assistance
Site visits
Feasibility studies
Assisting project owners
Assisting works contractors
Calculations and modelling
Expertise and experience for all trenchless projects
With cutting-edge skills and a team of experienced engineers, many from drilling / tunnelling backgrounds, OPTIMUM delivers innovative solutions for the design and monitoring of trenchless crossings, big and small.
OPTIMUM’s specialist engineering teams accompany its customers at every stage of their trenchless project, from the initial design through to works completion: feasibility studies, selecting the most appropriate trenchless technique, designing the associated structures,
developing the purchase strategy, …
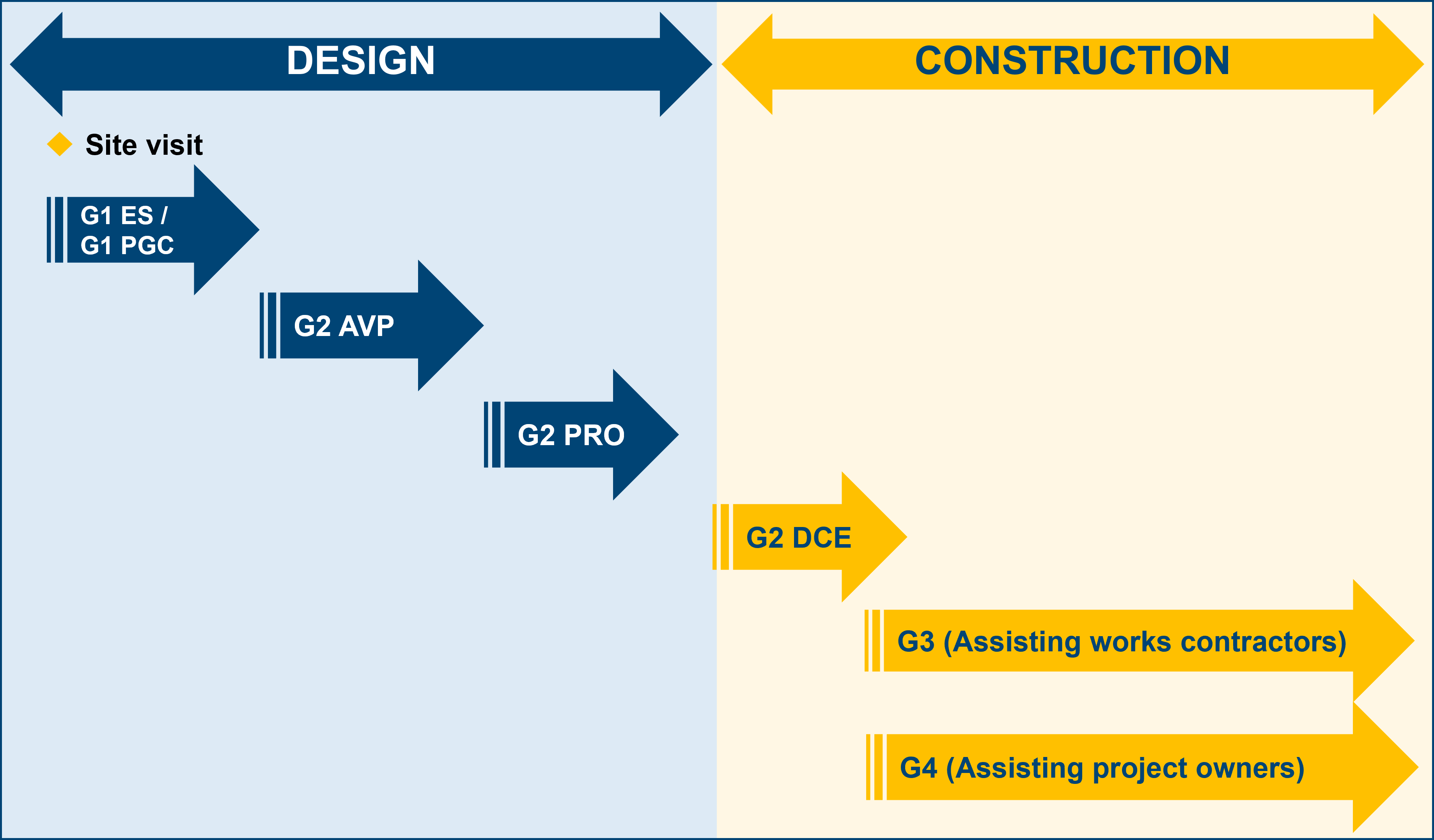
Site visits
A key stage in any trenchless project that allows for a better understanding of the context and constraints of the site.
Our site visit includes :
Discussions with the client on specific project constraints
Observation of the nature and elevation of the land
Identification of access roads, rights-of-way and potential job site locations
Identification of existing infrastructure (networks, obstacles, buildings).
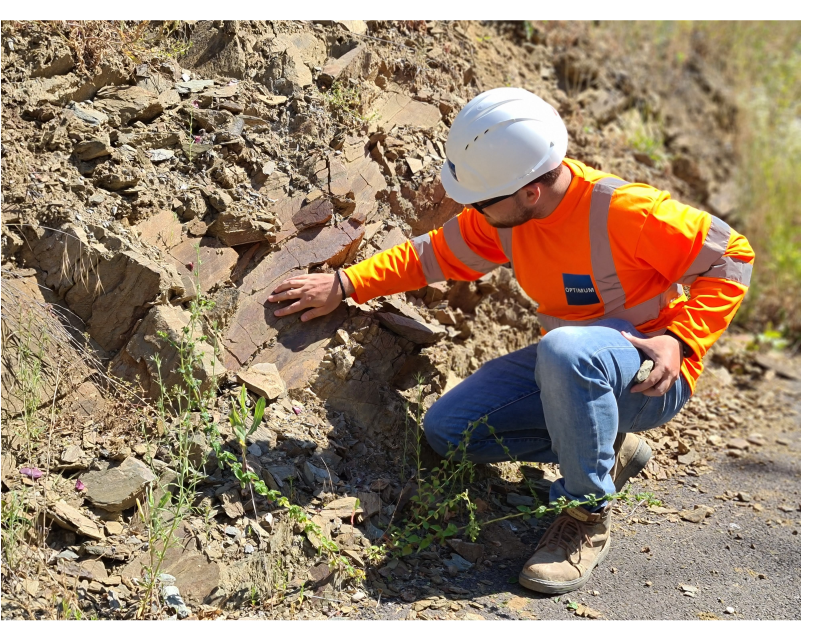
Trenchless feasibility studies
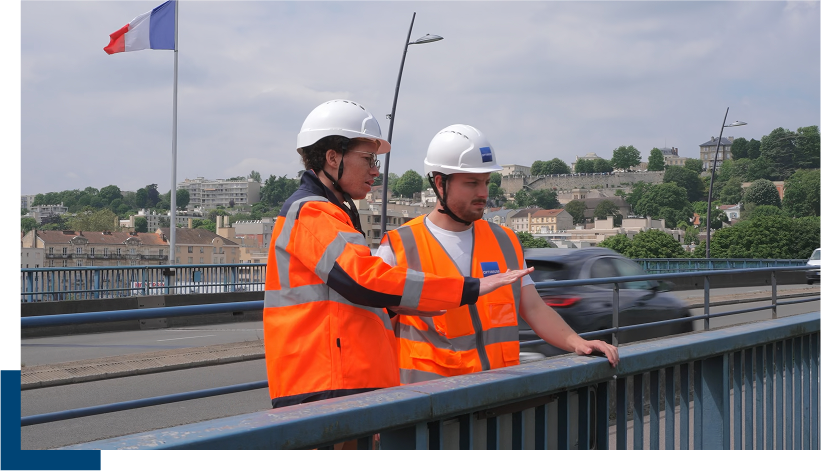
An approach ensuring study accuracy and relevance
The success of trenchless crossings depends on several factors, with the quality and relevance of the pre-construction study being one the most critical.
When developing trenchless crossing studies, OPTIMUM applies a method based on the French NFP94-500 norm, which not only simplifies the development of the project, but also increases the efficiency and relevance of the ground investigations. Thanks to their jobsite
experience, OPTIMUM engineers have a perfect understanding of all trenchless techniques,
therefore optimising this crucial study phase.
Conceptual (G1 ES / PGC) study
A preliminary study aimed at establishing a geotechnical /geological model of the site with a view to preparing the detailed design phase of the project.
Our Conceptual (G1 ES / PGC) study includes:
Analysis of available bibliographic / geological data
Selection of the most suitable trenchless technique
Definition of the general construction guidelines
Development of a programme of geotechnical investigations and laboratory tests to be carried out before the FEED (G2 PRO) study
If required, budgets and planning schedules can also be estimated at this stage.
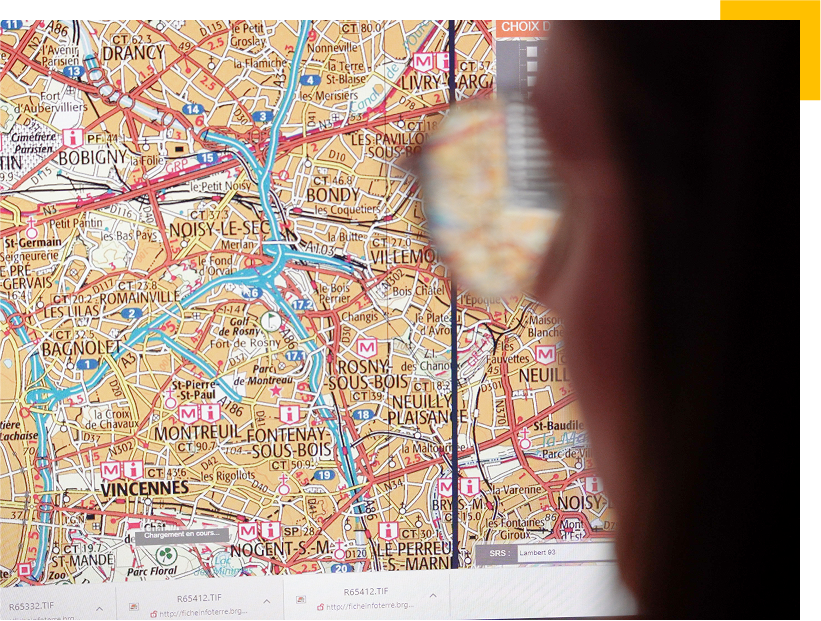
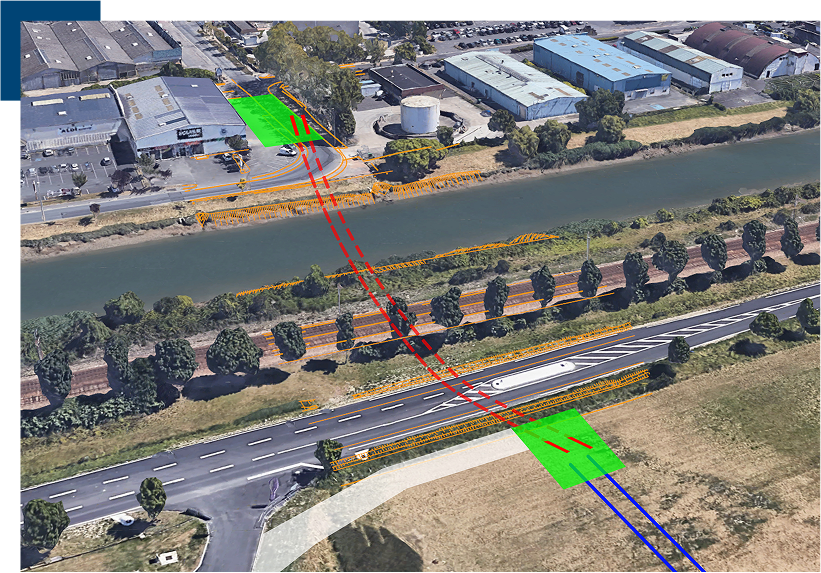
FEED (G2 PRO) study
A detailed feasibility study, drafted after receipt of the geotechnical investigations, which confirms or contests the hypotheses of the preliminary study.
Our FEED (G2 PRO) study includes:
Analysis of the results of geotechnical soil investigations
Definition of a soil model
Selection of the most appropriate trenchless technique
Definition of the technical parameters
Calculations and modelling
Sizing of the drilling / tunnelling equipment
Definition of the rights-of-way necessary for jobsite installation
Formulation of the preliminary modus operandi
Design of the crossing profile
Railway specific studies
A specific mission for crossings under SNCF railway tracks to precisely meet the strict design criteria.
Preparing a « TSV » dossier includes:
Drafting a dedicated risk analysis for the railway crossing
Verification of duct / pipe load resistance
Formulation of a protocol to ensure the integrity of the railway platform
Drafting a continuous, track alignment monitoring programme
Preparation of the complete dossier, in accordance with SNCF requirements
If required, OPTIMUM can also submit the dossier to the SNCF and handle negotiations until the necessary approvals have been received from SNCF Réseau.
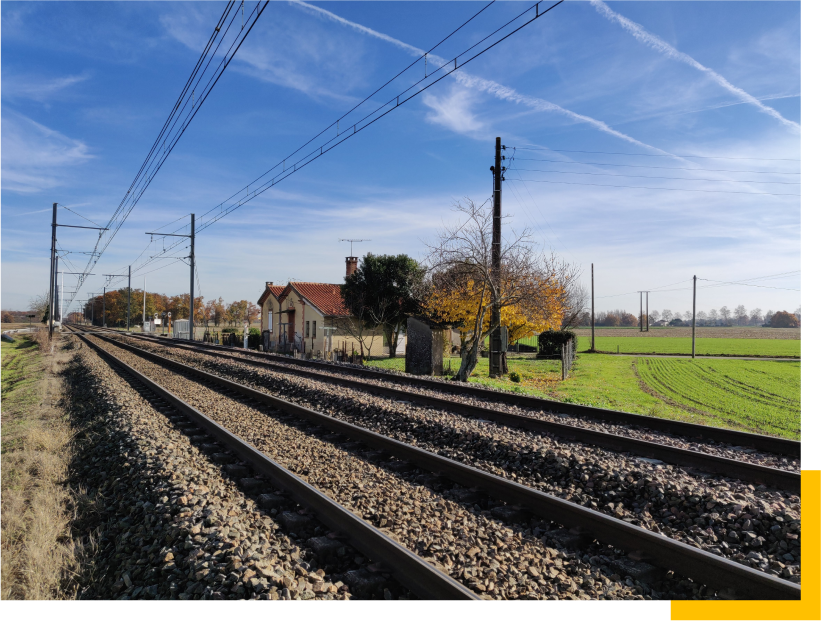
Assisting project owners
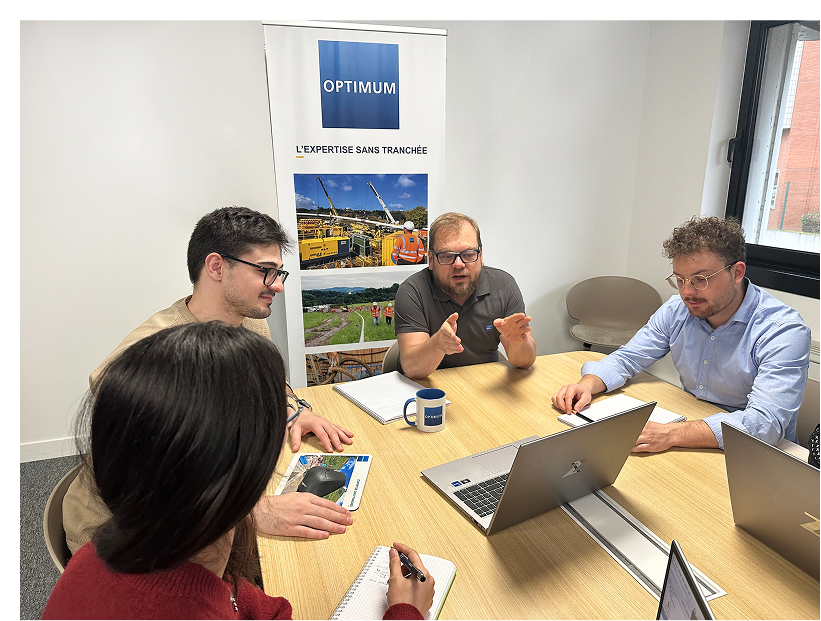
G2 DCE / ACT Mission
A mission to support the Project Owner and / or Project Manager during the contractor selection phase: pre-selecting companies capable of carrying out the works and assessing the technical validity of their proposals.
Our G2 DCE / ACT mission includes:
Selection of contractors able to carry out the requested drilling / tunnelling works
Drafting the technical chapters of tender documents
Analysis of technical submissions
Evaluation of the technical eligibility of each bid
Attending the bidders’ technical presentations
Establishing a final technical scorecard
G4 Mission
A supervisory mission to support the Project Owner and / or Project Manager during the works preparation and construction.
Our G4 mission includes:
Supervision of the contractors’ plans and procedures before works begin
Supervision of the construction phase, including:
kick-off meeting
supervision and control of onsite operations
daily analysis of technical parameters
identification and monitoring of discrepancies until resolution
Summary of the supervision conducted during the G4 mission, for inclusion in handover documents
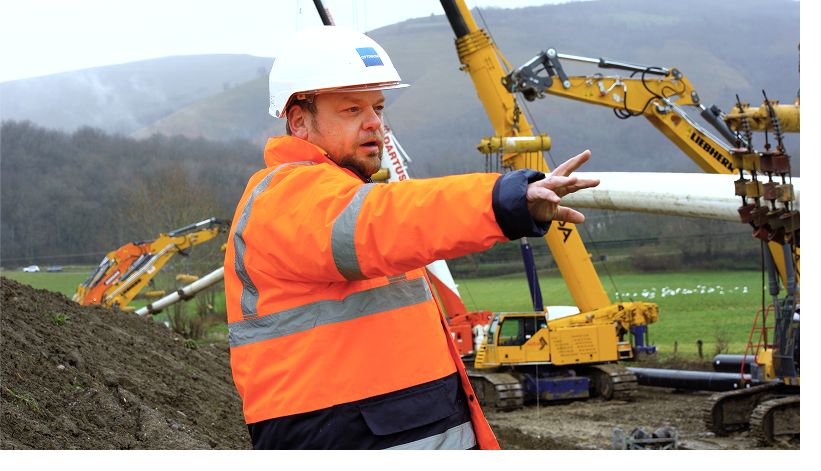
Assisting works contractors
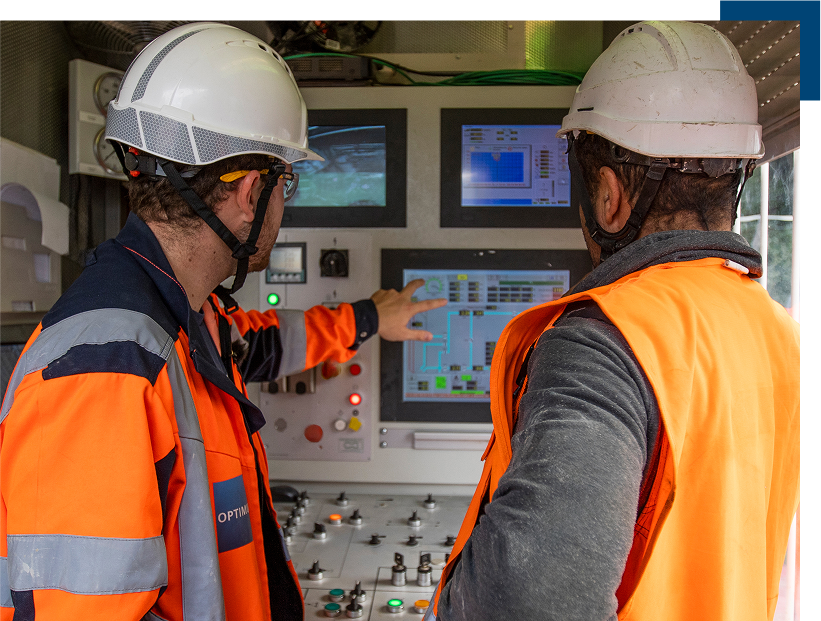
G3 Mission
A mission to support the works contractors directly to anticipate geotechnical risks and identify potential discrepancies during drilling / tunnelling works.
Our G3 mission includes:
Before works begin:
verification and analysis of geotechnical data
recommendation of additional soil investigations, if necessary
checking coherence between methodology and ground conditions
During the works:
continuous monitoring of drilling / tunnelling parameters
identification of potential discrepancies and definition of appropriate corrective measures
After the works:
preparation of the works completion report
Calculations and modelling
Calculations specific to each trenchless technique which allow for ground behaviour to be modelled so as not to impact the existing infrastructures during the works.
Based on industry and/or proprietary software, our calculations and modelling allow for:
Evaluation of the soil behaviour at each stage of construction
Evaluation of the force required to construct the trenchless structures and to install the final pipes / ducts
Modelling the reaction of soils and existing infrastructures to anticipate the likelihood and severity of identified risks
Designing end structures
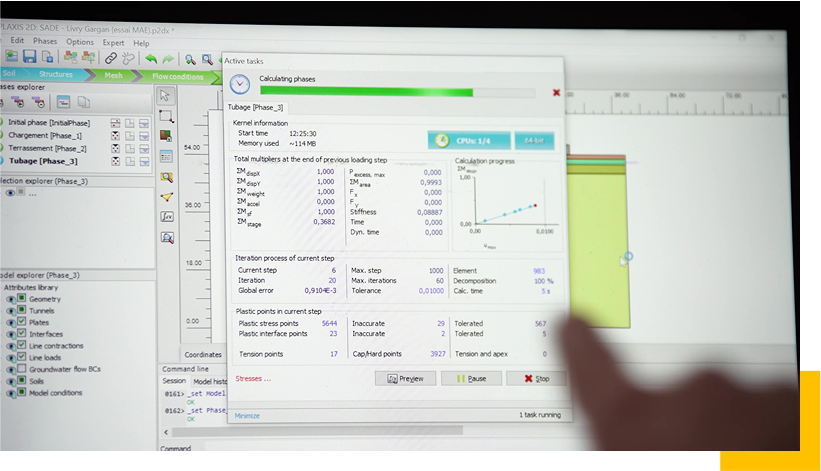
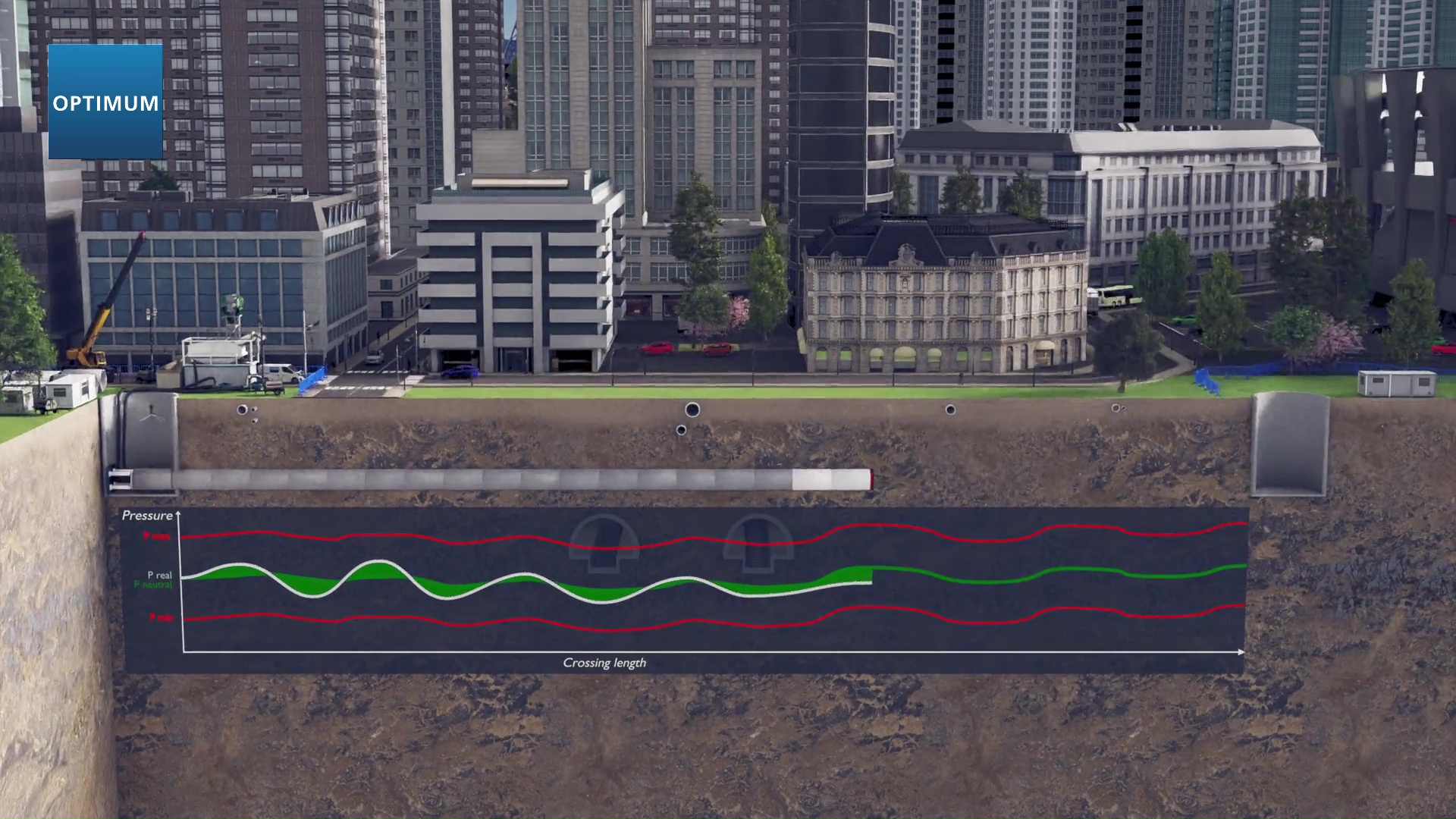
The importance of confinement pressure during microtunnelling operations
Confinement pressures must be continuously
monitored during microtunnelling operations to avoid breakouts and/or settlements
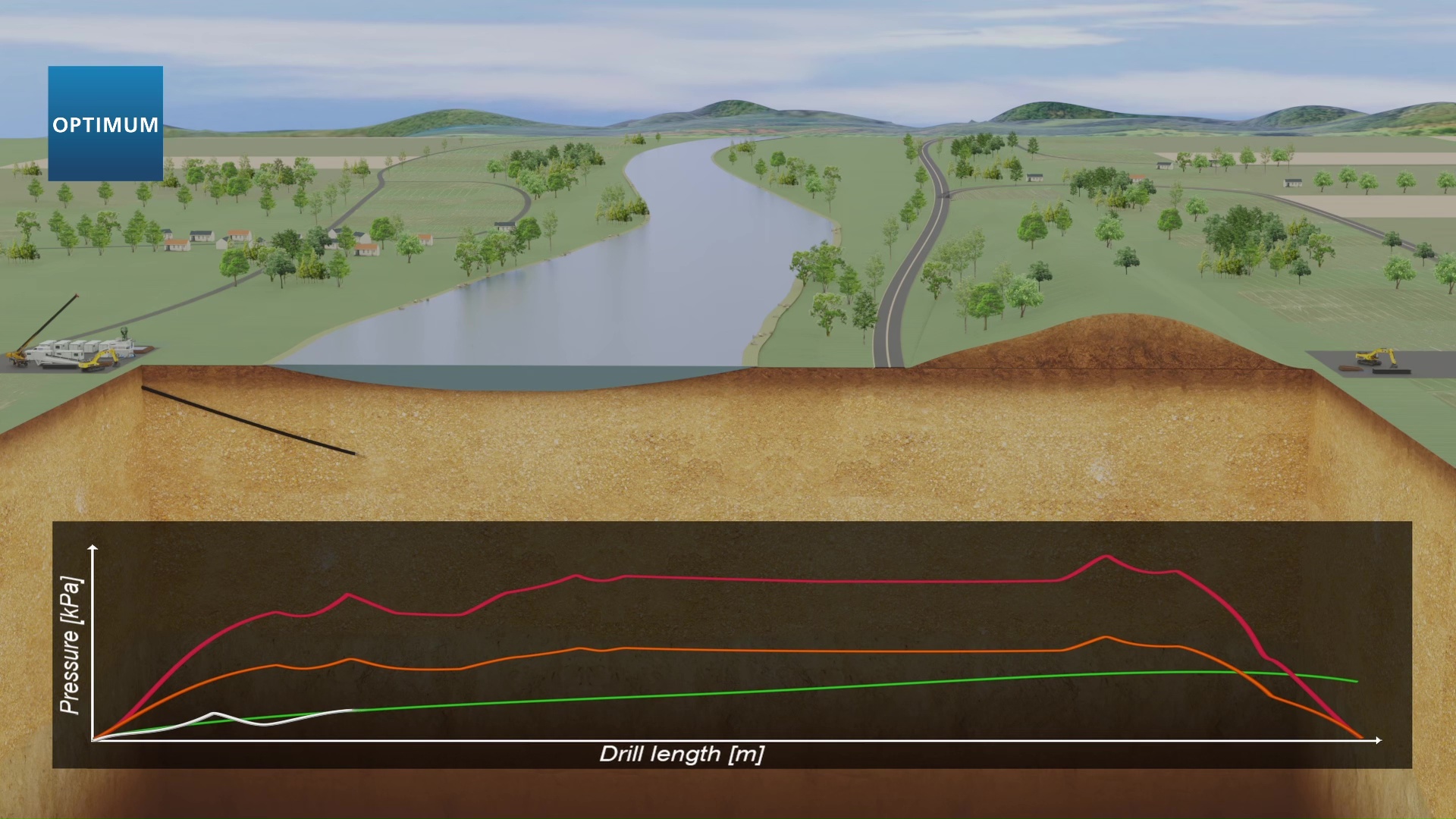
Limiting the risk of breakouts in HDD
Analysing geotechnical conditions allows potential drilling profiles and permissible fluid injection pressures to de determined and evaluated.
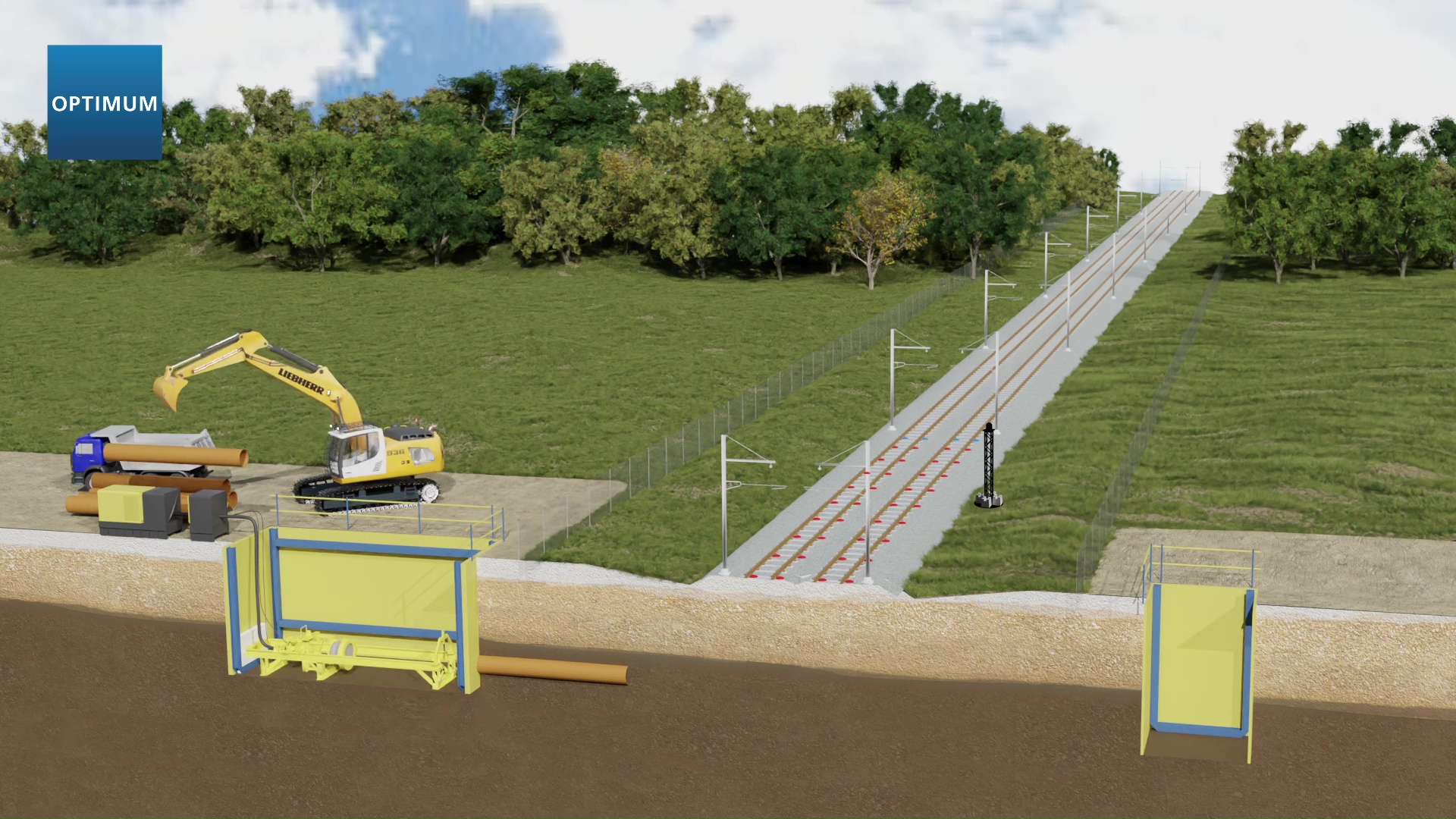
Minimising risks in trenchless crossings under railway lines
Crossing under railway tracks warrants particular attention; geotechnical aspects must be considered right from the design stage.